Vision X Takes LED Lighting Reliability to New Heights
- Mike Judd
- Dec 14, 2017
- 2 min read
Updated: May 10, 2019
A recent study of Vision X’s Heavy Industrial LED lighting shows their customers have been rewarded through outstanding performance, longevity and a reduction in unscheduled maintenance costs.

Vision X has taken many steps within its manufacturing process, quality controls, and sales process to ensure its customers are receiving the best product for the job. “With a phenomenal warranty rate at only 575 PPM (Parts Per Million) on our BHB line, we found that many of our customers are saving thousands of dollars on their job sites each year. Think about it, that’s only 1 warrantied product for every 2,000 parts that are being put through the most rugged environments from extreme temperatures to harsh environments in mining, public service fleets, and agricultural centers. In fact, we’ve reduced one of our customer’s unscheduled maintenance time by 80%, resulting in an approximate $28,500 savings in a single year. When you add in the cost of lights they had replaced along with maintenance labor, they realized a one-year cost reduction of $216,936.
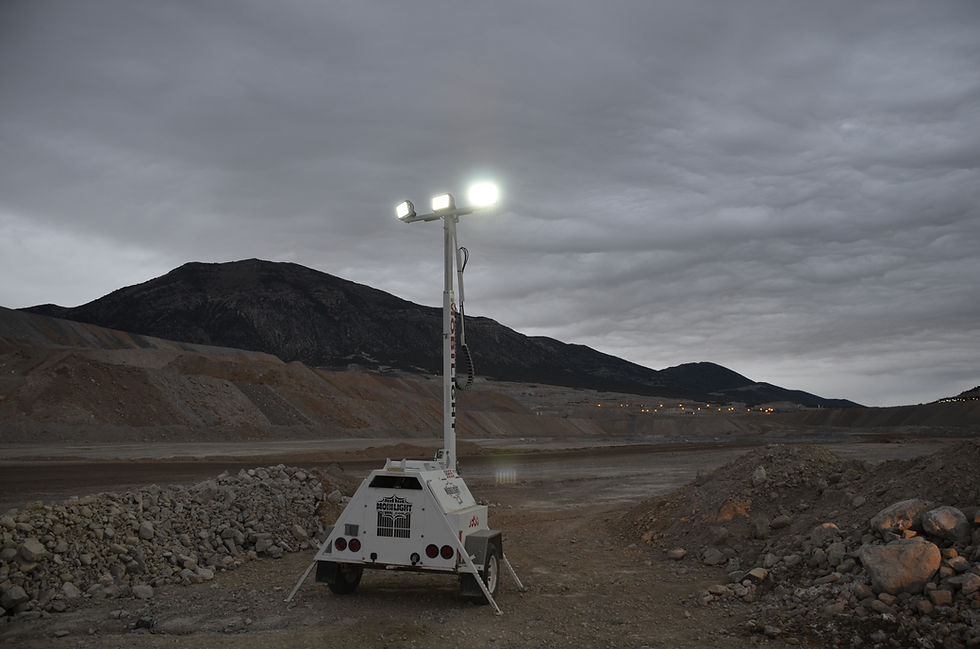
These numbers all come from real world use in these demanding conditions. We are making a difference in reducing operating costs for our customer base” – Mike Judd, Mining/Industrial Manager So how is it that Vision X is shining without failure? It starts from the foundation.

Rather than outsourcing the manufacturing process like so many LED brands do, which expose themselves to inconsistencies and poor oversight, Vision X controls their complete manufacturing process from Engineering to Shipping.
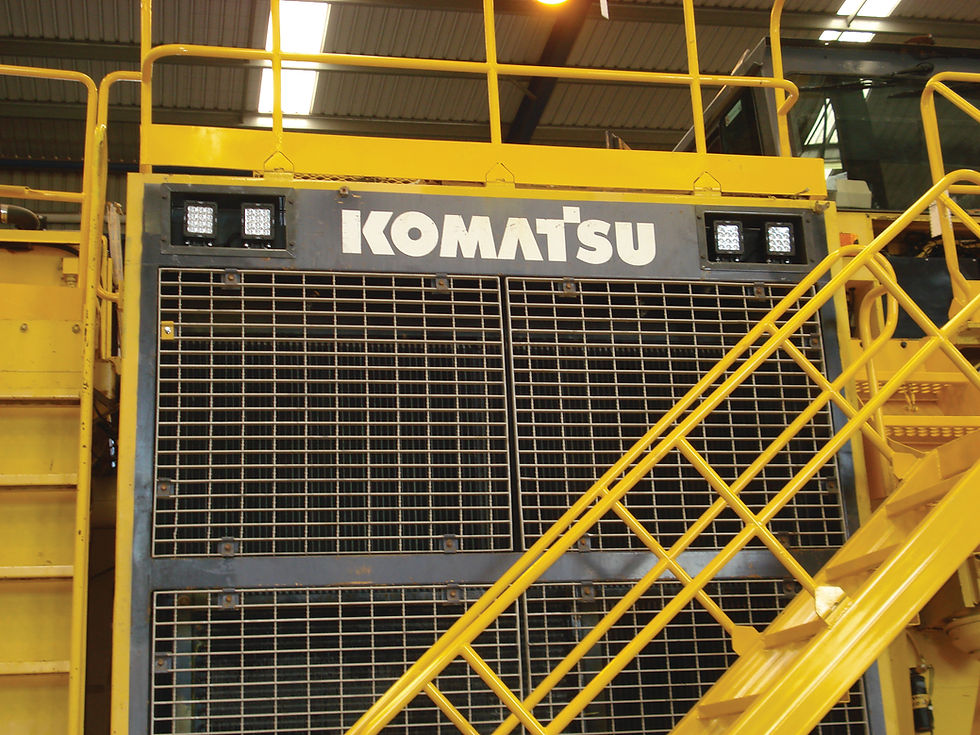
Vision X’s Steps to a long lasting, high performing LED Light fixture:
1. Engineer for the Application
2. Manufacture with high quality materials, coating, and Top Binned LEDs
3. Quality Control process including item tracking throughout
4. Extensive Batch Testing
5. Pre-Package Testing & Inspection for EVERY Light Fixture
6. Proper Education and Instruction with the Customer
7. Industry Leading Warranties for Highest Customer Satisfaction
Comentários